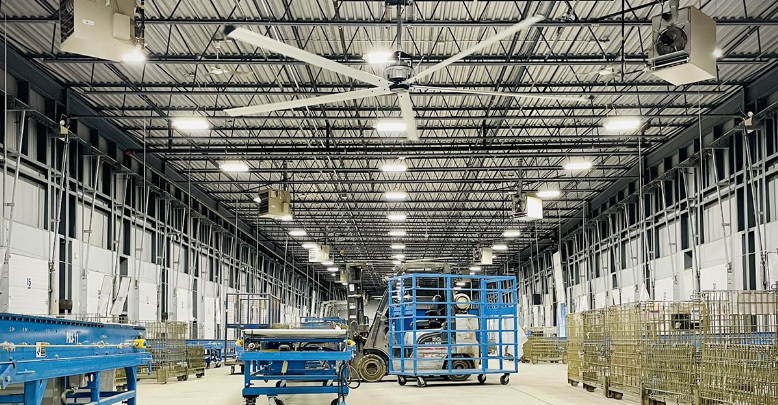
Industrial Fans are gaining popularity as a popular and affordable solution to boost air movement, limit heat stress, and create holistic better environmental control.
Whether you are the owner or an employee working at an industrial plant, manufacturing units, and other large-open industrial facilities, you would know the place witnesses a host of environmental control issues. For example, while in summer, the facilities can get frantically warm, in winter, it can cause the workers to shiver at the floor level, whereas heated air rises into the rafters. Not just this, they often need help with condensation, ventilation, zone-specific management, and other issues.
A building management system can mitigate these issues; a seasoned facility manager can leverage a mix of high-volume, low-speed fans and heat-stratified air layers to reach the goal. HVLS fans make HVAC systems efficient, which can significantly enhance employee comfort and health in all seasons. In addition, these fans can limit energy consumption, tackle air quality-related issues, and even combine fire prevention systems to make them more efficient.
Let’s Talk About the Seasonal Benefits of Industrial HVLS Fans.
The HVLS fans can be run in hot and cold weather, which has been proven in several studies. In steamy and harsh climatic conditions, industrial fans protect employees against heat stroke, exhaustion, and other heat-related situations by offering an evaporating cooling sensation and reducing cooling sensations considerably. In addition, the ambient environment provides an optimal working temperature for the workforce and enables the lowered setting of the AC system.
On the other hand, in winter months, the HVLS system can address the rising heat effect, achieved by the destratification of heated air layers, which circulate warm air from the ceiling back onto the ground and back to the working crowd. This is how HVLS fans cut down the burden on their heating system. Simply put, facilities equipped with HVLS fans generally don’t require a high-temperature set point to meet the necessary environmental comfort, decreasing energy consumption and saving money in the long run.
How can HVLS help Address Energy Efficiency and Costs?
We all know industrial fans play an important role in limiting energy costs. Typically, standard fans run faster than industrial fans, but industrial fans have bigger blades that can cover more surface area than traditional fans, delivering a more even flow of air.
Another fact that sets industrial fans apart from standard ceiling fans is that they are quieter than traditional models as they don’t derange the working process.
It is believed that the functioning capacity of one industrial fan is equivalent to 34 contemporary ceiling and tabletop fans. However, their specifically-designed airfoils and large circumferences allow them to save more energy than the standard fans, making them the best choice for big warehouses and open spaces.
Industrial fans can be used with air conditioning systems, resulting in around 25% less energy used by the HVAC system. In addition, since the industrial fans work with the HVAC system, they won’t incur much electricity.
This is a rough explanation of an industrial fan; let’s explore the intricacies that differentiate an industrial fan from a general-purpose plan. There is a massive difference between how industrial fans are designed and their performance, get to know them in the following section.
The main Difference between Industrial and General Fans!
General fans are made from less expensive materials and components designed for residential or light-duty commercial markets. These fans can be installed in homes, appliances, and small ventilation systems.
On the other hand, industrial fans are made with heavier and high-quality materials and components to operate for longer hours, supply higher airflow and pressure, and meet industrial ambient requirements.
Here are some significant differences between general-purpose fans and industrial fans.
Material Gauges – The general-purpose fans is made from light gauge sheet of metal and plastic. On the other hand, industrial fans are made from 10 gauges and plate materials made from cast aluminum and stainless steel.
Construction bearings – The general-purpose fans have tab and lock seams, sleeve or strap type, and short bearing life. Meanwhile, industrial fans include continuous welds with the ball or roller bearings in cast iron housing. As a result, construction bearing in industrial fans has a longer bearing life.
Motor – General purpose fans are light-duty, bears sleeve, and has minimal design features, and has an open drip-proof enclosure. On the other hand, industrial fan motors are heavy-duty, have special design features, and their service factors come with TEFC and EXP enclosures.
Safety factors – General purpose fans run with slower wheels and shaft speeds, while industrial fans have higher wheel and shaft speeds.
Airflow – General purpose fans have limited airflow limited to 2000 CFM or less, while in industrial fans, the airflow is limited from 200 to over 100,000 CFM.
Pressures – General purpose fans have 10” to 4.0” static pressures, while industrial fans range from 50” to over 100” static pressures.
Closing down!
In a nutshell, bigger industrial fans are better for large spaces because:
- It delivers better airflow.
- It enhances employee productivity by keeping the employees healthier.
- It results in low utility bills.
- It helps create a quiet work environment.
- It discards any chance for trip hazard.
- It delivers year-round value, irrespective of the season.
Don’t take it lightly, the selection of industrial fans for your large facility. A large industrial fan can bring positive changes to the facility’s utility bills, safety, and productivity. Therefore, it is a value-based decision to invest in quality industrial fans, which have the potential to reward you in the years to come! And if you have any queries regarding industrial fans, explore our previous blog posts or contact us for more information.